ARTICLES
SEPTEMBER 2023
ARE YOU ON A CHEMICAL SOUP DIET?
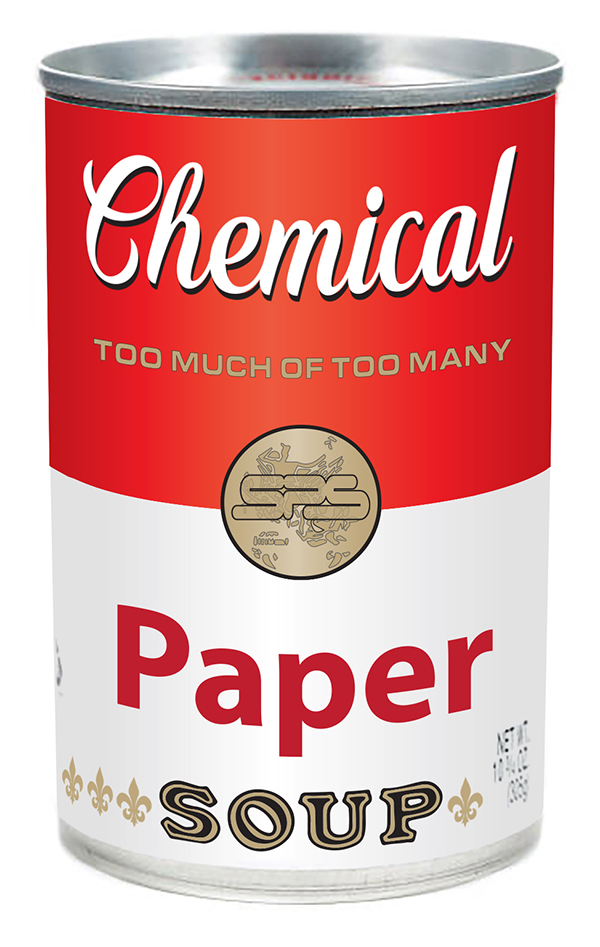
Papermaker's Signs Of Chemical Soup
Does your paper recipe cause
- High tray consistency?
- Low first pass/first pass ash retention?
- Low couch roll solids
- Weak, wet web and difficulty threading up?
- Foamy white water?
- Wet press breaks?
- Low press solids?
- High defoamer use?
- High wet end starch dose?
- High total additive cost?
- Hard drying?
- Thick, persistent foam in the basement, in the sewers, in the drains?
- Deposits, spots, holes?
- Dusting, linting, picking?
- High BOD/COD?
- Low or variable Scott Bond or Z-direction tensile?
- Low or variable sizing or COBB?
Then you may be making Chemical Soup!
“We are here to make paper, not chemical soup.”
In recent decades recycled fiber has become an ever more important source of raw material. With recycling comes a declining trend in fiber length and diminishing strength.
Concurrent with recycling, mills are reducing freshwater use, increasing the conductivity of the whitewater circuits. Consequently, more polymers and generally higher electrostatic charge density chemicals are being used to maintain retention, promote drainage and meet strength specifications.
All these factors trend toward higher total use of chemical aides and starch. But there is a point of diminishing return, and it arrives very quickly, frequently unrecognized. To achieve steady-state production and consistent quality from your papermaking recipe, use judicious helpings of cationic starch and carefully measured, selected chemical to achieve a balanced blend that maximizes the performance and synergy of all your additives.
Contact Bob Howard To Learn About Starch Performance Services’ recipe to prevent Chemical Soup Indigestion.
AUGUST 2023
CATIONIC STARCH IS NOT A COMMODITY, IT’S THE SUPERHERO
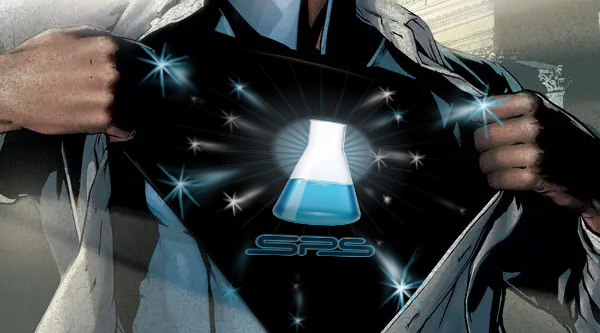
Mild mannered starch transforms into a powerful paper-making ingredient.
Cationic starch is a highly functional specialty additive that is made by chemically modifying a commodity base product…starch.
In the manufacturing of paper, cationic “wet end” starch is one of the most widely used additives to achieve fiber flocculation, fines and filler retention, efficient dewatering of the pulp, and improved sheet strength. It is a one-stop additive for delivering all but the most demanding properties for paper machine runnability and paper quality.
But not all starches are created equal. Cationic starch performance can differ significantly depending on the choice between the most widely available commercial starches: corn, wheat, waxy maize, potato and tapioca. The difference in performance between these starches is mostly inherent in the molecular weight, structure and distribution naturally occurring in these individual starches.
A second, less-appreciated difference in the performance of any wet end starch can be importantly manipulated by the preparation, storage, and delivery of starch to the paper pulp. This includes cooking the starch at the lowest practical temperature to achieve complete pasting, cooking in the solids range of 4% to 8%, storing the cooked starch as close to 55° C as possible, and delivering the starch to the pulp stream at 0.8% to 1.5% solids at the optimum addition point with good mixing.
The goal on most paper machines should be to achieve
- the maximum machine speed,
- the maximum press dewatering,
- and lowest drier steam pressure
- with the lowest dose (lowest cost) of chemical additives possible.
Following the steps above will help the starch to deliver the maximum paper-making properties with the least amount of starch and chemical additives.
For more information and help to lower the total cost of paper manufacturing on your machine, contact Bob Howard at STARCH PERFORMANCE SERVICES.
It is the mission of Starch Performance Services to help you maximize the value from your starch.